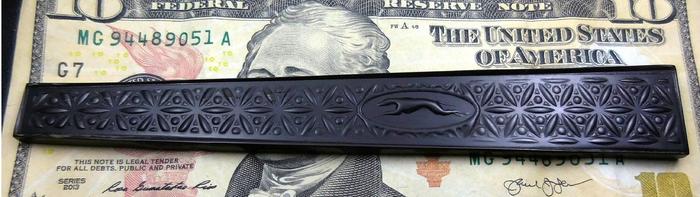
Having read everything I could on the internet and other sources on the old methods of pressing horn, I finally, after much experimentation, have gotten to where I can at least produce a reasonable facsimile of the older work. Making the horn pliable can be achieved by boiling, flaming, baking, and heat lamps, but each of those methods has serious drawbacks when trying to align a piece of hot horn to a cold die, and then press it. The solution is to heat the horn and the die together as a unit. More experimentation (read as failures) based on that concept, led me to making this fixture.
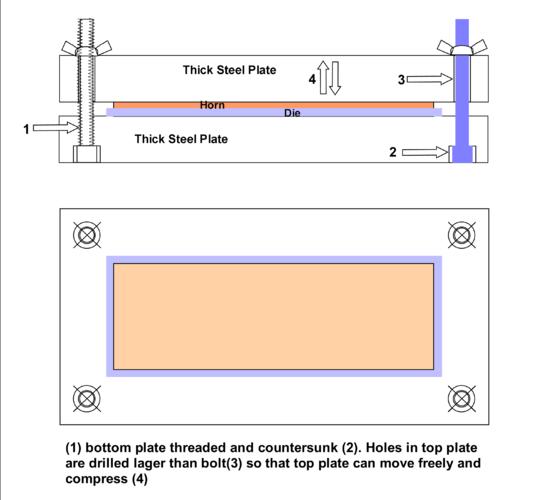
The top plate moves up and down freely, which allows for compression once the fixture is in the press. The wing nuts tighten the horn and die firmly together in the cold state. Keeping the horn and die aligned is very important, and high temperature tapes can be used to initially locate and fix the two until the top plate is affixed and tightened. Once tightened down, the unit can be handled without affecting the line-up, and that is a key feature. BTW this is heavy. If I had a better press, the weight could be lowered a bit.
I am still logging values for optimal temperatures and times, but my examples were made by heating the fixture to 450 degrees for about 45 minutes. The time is to make sure that the fixture and contents are all at temperature. I use the kitchen oven, and no, it doesn’t smell. It’s ready when a toothpick inserted into the middle comes out clean…..oh, wait a minute, that’s a cake, never mind.
I don’t have the perfect press, but I have an old arbor press fitted with a 12 ton jack. That it has a single point ram is not the best configuration, but I can get it to work by pressing different areas. The wing nuts on the fixture can be tightened once compression loosens them, so I can then move it around. A good press would be a heavy duty rectangle of steel with two jacks mounted side by side. 6 ton jacks would probably work. There is lots of experimentation and designing left for the reader to explore. I have had areas end up not being deep enough, and you can realign, reheat and repress.
Once the horn has been pressed, the fixture is left under pressure until cool. You can speed that up with fans and laying aluminum bars on the fixture to act as heat sinks.
There is much to say about the dies, and the artwork for the dies, but to keep this from being overly long I’ll answer questions about that as they are asked. In short, I’m using photo etched magnesium alloy dies obtained from Owosso Engraving Company. I can’t say enough good things about them. The dies generally cost around $50 for the 2-up size. They can even make hand engraved dies that could emulate the finely detailed work of the past, but they would be very expensive. The art used for making the dies needs to be black and white vector based artwork. I have been asking for a 3/32” depth, but may move back to 1/16”. Whether something is right reading or wrong reading is also very important. I made a mistake on the greyhound die. I had just flipped it around to make the second image. I should have mirrored it. The greyhound is upside down on the read side of the razor @@##@#. The correct die is in the mail. Who knew a dog could be right or wrong reading?
Blank dies can also be made that slightly impress the back of the horn over the design area on the other side of the horn. These can be made from thin sheet metal, or you could order an etched one. Even a layer of thin tape will make an impression. A random pattern of bits and pieces could be pressed into and all over a whole piece of horn, and not require a die. There is very much to play with. Just remember that what is etched into the die will be raised on the horn. Get a good pair of oven mitts.
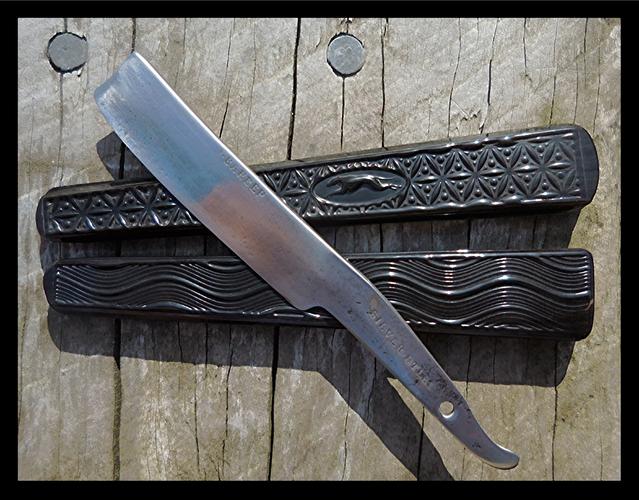